In de granulatie-industrie, of het nu gaat om een pelletiseermachine met een vlakke matrijs of een pelletiseermachine met een ringmatrijs, is het werkingsprincipe gebaseerd op de relatieve beweging tussen de drukrolmantel en de mal om het materiaal te grijpen en in het effectieve station te laten komen, het in vorm te extruderen en het vervolgens met het snijblad in deeltjes van de gewenste lengte te snijden.
Deeltjespersrolmantel
De drukrolmantel bestaat hoofdzakelijk uit een excentrische as, wentellagers, een drukrolmantel die om de drukrolas is aangebracht en onderdelen die de drukrolmantel ondersteunen en bevestigen.
De drukrolmantel perst het materiaal in het matrijsgat en vormt het onder druk in het matrijsgat. Om slippen van de drukrol te voorkomen en de grijpkracht te vergroten, moet er een zekere wrijvingskracht zijn tussen de drukrol en het materiaal. Daarom worden er vaak maatregelen genomen om de wrijving en slijtvastheid te verhogen op het oppervlak van de drukrol. Bij het bepalen van de structurele parameters van de drukrol en de matrijs, hebben de structurele vorm en grootte van het buitenoppervlak van de drukrol een aanzienlijke invloed op de granulatie-efficiëntie en deeltjeskwaliteit.
Oppervlaktestructuur van de drukrolmantel
Er zijn drie veelvoorkomende oppervlaktetypen voor de bestaande deeltjespersrollen: gegroefd roloppervlak, gegroefd roloppervlak met randafdichting en honingraatroloppervlak.
De drukrol met getande groef heeft goede rolprestaties en wordt veel gebruikt in veevoer- en pluimveevoerfabrieken. Door het glijden van het voer in de getande groef is de slijtage van de drukrol en de ringmal echter niet gelijkmatig en is de slijtage aan beide uiteinden van de drukrol en de ringmal ernstiger.
De getande groef-aandrukrol met randafdichting is vooral geschikt voor de productie van aquatische materialen. Aquatische materialen hebben een grotere neiging tot glijden tijdens de extrusie. Dankzij de randafdichting aan beide zijden van de getande groef is het niet gemakkelijk om naar beide kanten te glijden tijdens de extrusie van het voer, wat resulteert in een gelijkmatigere verdeling van het voer. De slijtage van de aandrukrol en de ringmal is ook gelijkmatiger, wat resulteert in een consistentere lengte van de geproduceerde pellets.
Het voordeel van de honingraatrol is dat de slijtage van de ringvorm gelijkmatig is en de lengte van de geproduceerde deeltjes relatief consistent is. De prestaties van de rol zijn echter slecht, wat de output van de granulator beïnvloedt en minder gebruikelijk is dan het gebruik van sleufrollen in de productie.
Hieronder vindt u een overzicht van 10 typen drukrollen voor deeltjesmachines voor Baoshell-ringmatrijzen. De laatste 3 heeft u absoluut nog niet gezien!
NR. 10 Groeftype
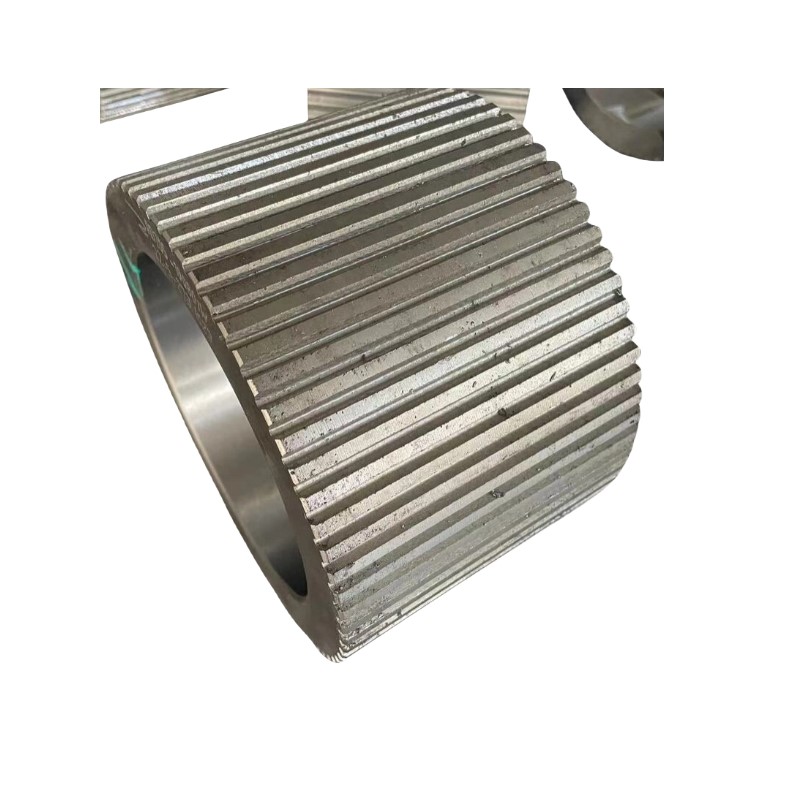
Nr. 9 Gesloten groeftype
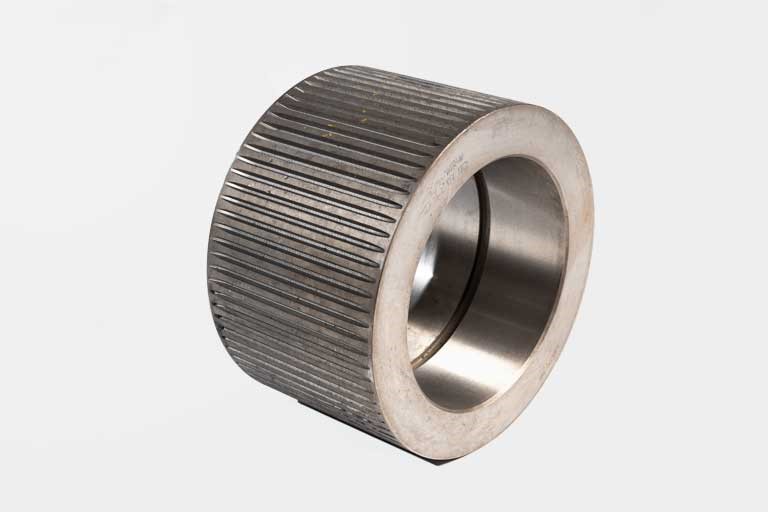
Nr. 8 Honingraattype
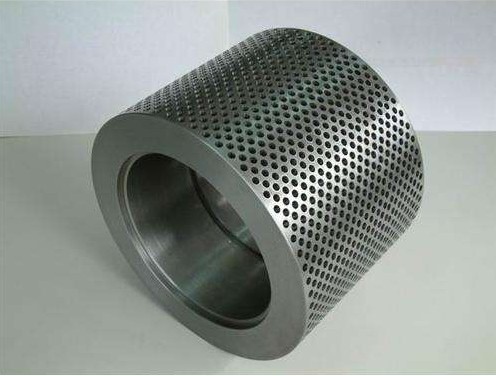
NR. 7 Ruitvormig
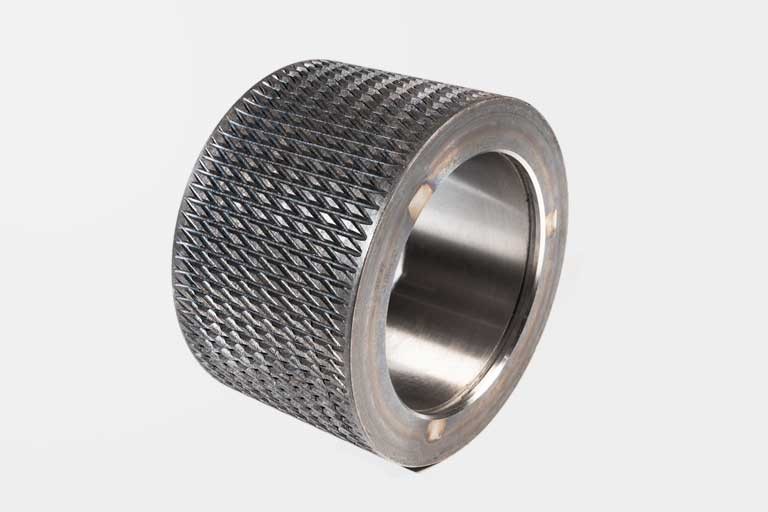
NR. 6 Schuine groef
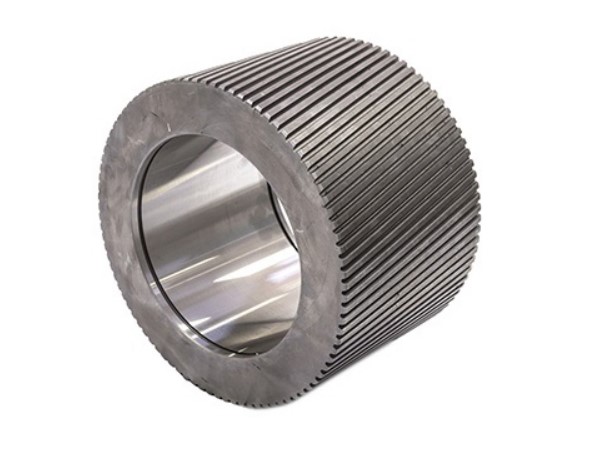
NR. 5 Groef + honingraat
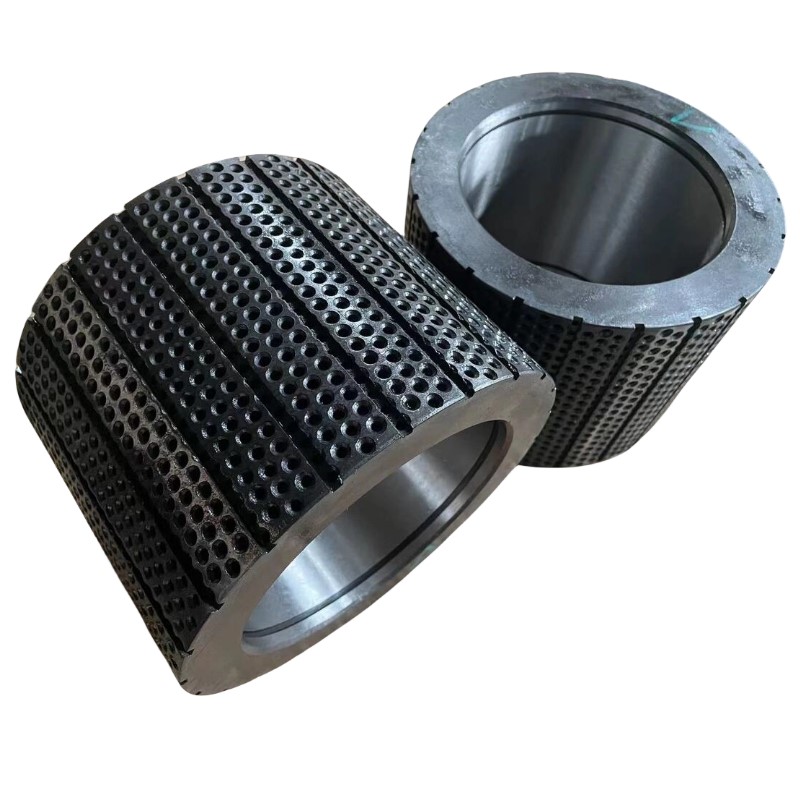
NR. 4 Gesloten groef + honingraat
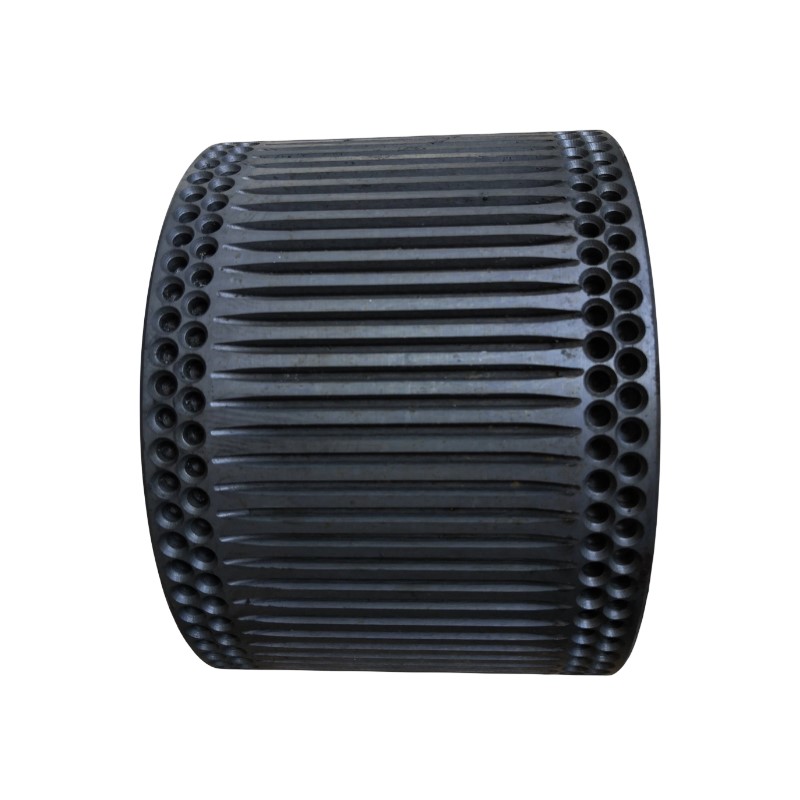
NR. 3 Schuine groef + honingraat
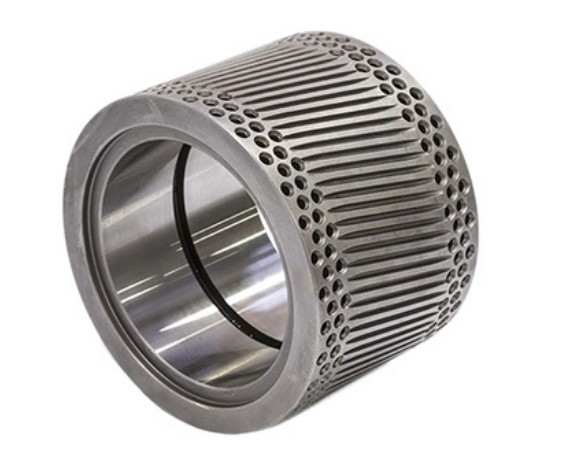
Nr. 2 Visgraatrimpeling
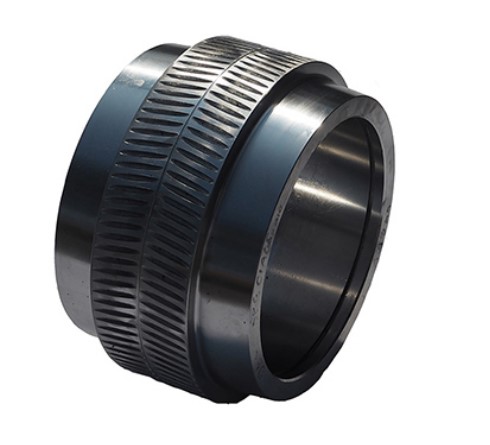
NR. 1 Boogvormige rimpel
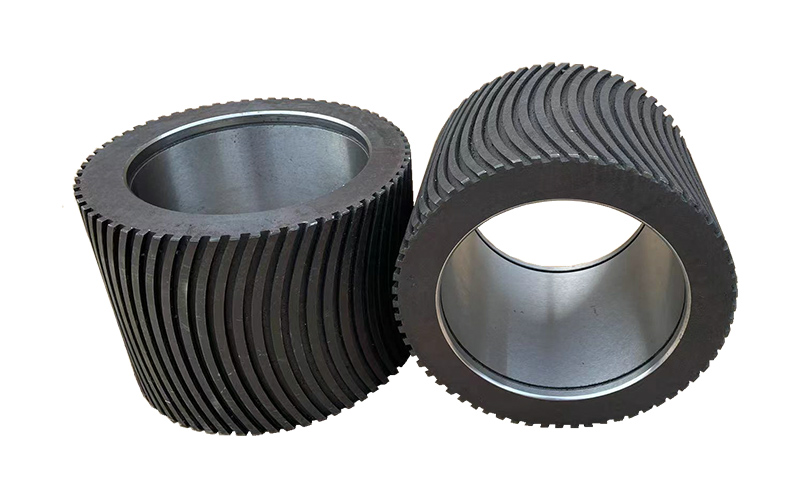
SPECIAAL MODEL: TUNGSTEN CARBIDE COLLER SHELL
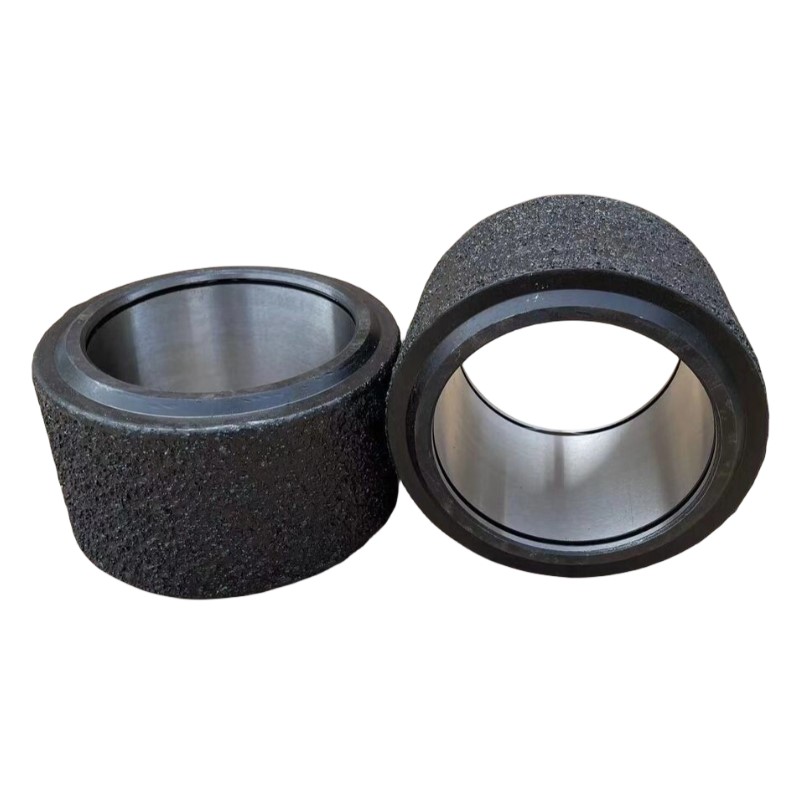
Behandelingsmethode voor het slippen van de drukrol van de deeltjesmachine
Vanwege de zware werkomgeving, de hoge werkintensiteit en de snelle slijtage van de drukrolmantel is de drukrol een kwetsbaar onderdeel van de deeltjesmachine en moet deze regelmatig worden vervangen. Uit de productiepraktijk is gebleken dat slippen van de drukrol van de deeltjesmachine kan optreden zolang de eigenschappen van de productiematerialen veranderen of andere omstandigheden tijdens het verwerkingsproces veranderen. Raak niet in paniek als de drukrol slipt tijdens het granulatieproces. Raadpleeg voor meer informatie de volgende technieken:
Reden 1: Slechte concentriciteit van de drukrol en spindelinstallatie
Oplossing:
Controleer of de montage van de drukrollagers verstandig is, om te voorkomen dat de drukrolmantel naar één kant afwijkt.
Reden 2: De belvormige mond van de ringmal is vlak geslepen, waardoor de mal geen materialen opeet
Oplossing:
Controleer de slijtage van de klemmen, transmissiewielen en voeringringen van de granulator.
Pas de concentriciteit van de ringmalinstallatie aan, met een afwijking van maximaal 0,3 mm.
De afstand tussen de aandrukrollen moet zo worden afgesteld dat de helft van het werkoppervlak van de aandrukrollen met de mal samenwerkt. Ook het wieltje voor het instellen van de afstand en de borgschroef moeten goed werken.
Wanneer de aandrukrol slipt, mag u de deeltjesmachine niet te lang stationair laten draaien en mag u niet wachten tot de machine zelf het materiaal afvoert.
De compressieverhouding van de gebruikte ringvormige malopening is te hoog, wat een hoge materiaalafvoerweerstand van de mal veroorzaakt en ook een van de redenen is voor het slippen van de drukrol.
De pelletiseermachine mag niet onnodig stationair draaien zonder dat er materiaal wordt aangevoerd.
Reden 3: Het drukrollager zit vast
Oplossing:
Vervang de drukrollagers.
Reden 4: De drukrolbehuizing is niet rond
Oplossing:
De kwaliteit van de rolbehuizing is onvoldoende, vervang of repareer de rolbehuizing.
Wanneer de aandrukrol slipt, moet deze tijdig worden gestopt om te voorkomen dat de aandrukrol te lang stationair blijft draaien.
Reden 5: Buigen of losraken van de drukrolspindel
Oplossing:
Vervang of draai de spindel vast en controleer de staat van de spindel van de drukrol wanneer u de ringmal en de drukrol vervangt.
Reden 6: Het werkoppervlak van de drukrol is relatief niet uitgelijnd met het werkoppervlak van de ringvorm (randkruising)
Oplossing:
Controleer of de aandrukrol verkeerd is gemonteerd en vervang deze.
Controleer of de excentrische as van de aandrukrol vervormd is.
Controleer de slijtage van de hoofdaslagers of bussen van de deeltjesmachine.
Reden 7: De spindelspeling van de granulator is te groot
Oplossing:
Controleer de speling van de granulator.
Reden 8: Het stanspercentage van de ringvorm is laag (minder dan 98%)
Oplossing:
Gebruik een pistoolboor om door het gat in de mal te boren, of kook het in olie en maal het fijn voordat u het invoert.
Reden 9: De grondstoffen zijn te grof en hebben een hoog vochtgehalte
Oplossing:
Zorg ervoor dat het vochtpercentage rond de 15% blijft. Als het vochtpercentage van de grondstoffen te hoog is, kan de mal verstopt raken en gaan schuiven nadat de grondstoffen in de ringvorm zijn gekomen. Het vochtregulatiebereik van de grondstoffen ligt tussen de 13 en 20%.
Reden 10: Nieuwe schimmel voedt zich te snel
Oplossing:
Pas de snelheid aan om te controleren of de aandrukrol voldoende grip heeft, voorkom dat de aandrukrol slipt en controleer tijdig de slijtage van de ringmal en de aandrukrol.
Plaatsingstijd: 25-03-2024