Slechte waterbestendigheid, oneffen oppervlak, hoog poedergehalte en ongelijkmatige lengte? Veelvoorkomende problemen en verbetermaatregelen bij de productie van aquatisch voer.
Bij onze dagelijkse productie van aquatisch voer zijn we op verschillende manieren problemen tegengekomen. Hier zijn enkele voorbeelden om met iedereen te bespreken:
1、 Formule
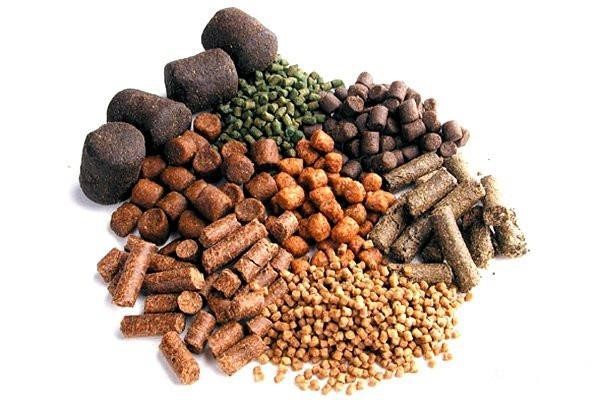
1. In de formulestructuur van visvoer zijn er meerdere soorten meelgrondstoffen, zoals raapzaadmeel, katoenmeel, enz., die tot de ruwe celstof behoren. Sommige oliefabrieken beschikken over geavanceerde technologie, waardoor de olie in principe droog wordt gebakken met een zeer laag gehalte. Bovendien zijn deze grondstoffen moeilijk te absorberen tijdens de productie, wat een grote impact heeft op de granulatie. Bovendien is katoenmeel moeilijk te vermalen, wat de efficiëntie beïnvloedt.
2. Oplossing: Het gebruik van koolzaadkoek is toegenomen en hoogwaardige lokale ingrediënten zoals rijstzemelen zijn aan de formule toegevoegd. Daarnaast is tarwe toegevoegd, dat ongeveer 5-8% van de formule uitmaakt. Door aanpassingen is het granulatie-effect in 2009 relatief optimaal en is de opbrengst per ton ook toegenomen. De 2,5 mm deeltjes liggen tussen de 8-9 ton, een toename van bijna 2 ton ten opzichte van voorheen. Ook het uiterlijk van de deeltjes is aanzienlijk verbeterd.
Om de efficiëntie van het vermalen van katoenzaadmeel te verbeteren, mengden we katoenzaadmeel en raapzaadmeel in een verhouding van 2:1 vóór het vermalen. Na verbetering was de vermalingssnelheid vrijwel gelijk aan de vermalingssnelheid van raapzaadmeel.
2、 Oneffen oppervlak van deeltjes
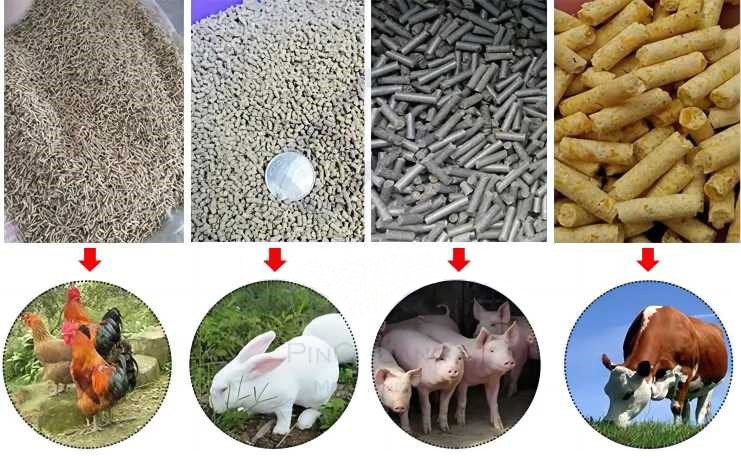
1. Het heeft een grote impact op het uiterlijk van het eindproduct en wanneer het aan water wordt toegevoegd, is het gevoelig voor instorting en heeft het een lage benuttingsgraad. De belangrijkste reden hiervoor is:
(1) De grondstoffen worden te grof gemalen en tijdens het temperingsproces worden ze niet volledig gerijpt en verzacht, en kunnen ze niet goed worden gecombineerd met andere grondstoffen wanneer ze door de gaten in de mal gaan.
(2) Bij de visvoerformule met een hoog gehalte aan ruwe vezels ontstaan er stoombellen in de grondstof tijdens het temperingsproces. Deze bellen barsten door het drukverschil tussen de binnen- en buitenkant van de mal tijdens het comprimeren van de deeltjes, waardoor het oppervlak van de deeltjes ongelijkmatig wordt.
2. Behandelingsmaatregelen:
(1) Controleer het verbrijzelingsproces op de juiste manier
Momenteel gebruikt ons bedrijf voor de productie van visvoer micropoeder met een zeefdikte van 1,2 mm als bulkgrondstof. We controleren de gebruiksfrequentie van de zeef en de mate van slijtage van de hamer om de fijnheid van het breken te garanderen.
(2) Regel de stoomdruk
Volgens de formule moet de stoomdruk tijdens de productie redelijk worden aangepast, doorgaans rond de 0,2. Vanwege de grote hoeveelheid grove vezelgrondstoffen in de visvoerformule zijn stoom van hoge kwaliteit en een redelijke tempertijd vereist.
3、 Slechte waterbestendigheid van deeltjes
1. Dit type probleem komt het meest voor in onze dagelijkse productie en heeft over het algemeen te maken met de volgende factoren:
(1) Een korte tempertijd en een lage tempertemperatuur resulteren in een ongelijkmatige of onvoldoende tempering, een lage rijpingsgraad en onvoldoende vocht.
(2) Onvoldoende kleefstoffen zoals stijfsel.
(3) De compressieverhouding van de ringmal is te laag.
(4) Het oliegehalte en het aandeel ruwe vezelgrondstoffen in de formule zijn te hoog.
(5) Factor voor de grootte van de verbrijzelende deeltjes.
2. Behandelingsmaatregelen:
(1) Verbeter de stoomkwaliteit, pas de hoek van de bladen van de regelaar aan, verleng de tempertijd en verhoog het vochtgehalte van de grondstoffen op de juiste manier.
(2) Pas de formule aan, verhoog de hoeveelheid zetmeelgrondstoffen op passende wijze en verminder het aandeel vet en ruwe vezels als grondstof.
(3) Voeg indien nodig lijm toe. (Bentoniet op natriumbasis)
(4) Verbeter de compressieverhouding van deringmatrijs
(5) Controleer de fijnheid van het vermalen goed
4、 Overmatig poedergehalte in deeltjes
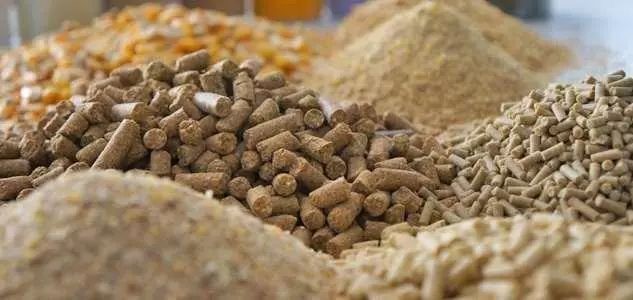
1. Het is moeilijk om het uiterlijk van de pellets na afkoeling en vóór het zeven te garanderen. Klanten hebben gemeld dat er meer fijne as en poeder in de pellets zit. Op basis van bovenstaande analyse denk ik dat hier verschillende redenen voor zijn:
A. Het oppervlak van de deeltjes is niet glad, de insnijding is niet netjes en de deeltjes zitten los en zijn gevoelig voor poederproductie;
B. Onvolledige screening door het graderingsscherm, verstopt schermgaas, ernstige slijtage van rubberen ballen, niet-passende schermgaasopening, enz.;
C. Er is veel fijne asresten in het magazijn voor het eindproduct en de opruiming is niet grondig;
D. Er zijn verborgen gevaren bij het verwijderen van stof tijdens het verpakken en wegen;
Behandelingsmaatregelen:
A. Optimaliseer de formulestructuur, selecteer de ringmatrijs verstandig en controleer de compressieverhouding goed.
B. Controleer tijdens het granulatieproces de tempertijd, de hoeveelheid toevoer en de granulatietemperatuur om de grondstoffen volledig te laten rijpen en zachter te maken.
C. Zorg ervoor dat de deeltjes een nette doorsnede hebben en gebruik een zacht snijmes van stalen strip.
D. Pas het beoordelingsscherm aan en onderhoud het, en gebruik een redelijke schermconfiguratie.
E. Door gebruik te maken van secundaire zeeftechnologie in het magazijn voor eindproducten, kan de poedergehalteverhouding aanzienlijk worden verlaagd.
F. Het is noodzakelijk om het magazijn en de kringloop van het eindproduct tijdig schoon te maken. Daarnaast is het noodzakelijk om de verpakkings- en stofverwijderingsapparatuur te verbeteren. Het gebruik van onderdruk voor stofverwijdering is het meest ideaal. Vooral tijdens het verpakkingsproces moet de verpakkingsmedewerker regelmatig de buffertrechter van de verpakkingsweegschaal uitkloppen en stofvrij maken..
5、 De lengte van de deeltjes varieert
1. Bij de dagelijkse productie stuiten we vaak op problemen met de besturing, vooral bij modellen boven de 420. De redenen hiervoor kunnen grofweg als volgt worden samengevat:
(1) De hoeveelheid voer voor granulatie is ongelijkmatig en het tempereffect fluctueert sterk.
(2) Ongelijkmatige spleet tussen de malrollen of ernstige slijtage van de ringmal en de drukrollen.
(3) Langs de axiale richting van de ringvorm is de afvoersnelheid aan beide uiteinden lager dan in het midden.
(4) Het drukverlagende gat van de ringvorm is te groot en de openingssnelheid is te hoog.
(5) De positie en hoek van het snijblad zijn onredelijk.
(6) Granulatietemperatuur.
(7) Het type en de effectieve hoogte (bladbreedte, breedte) van het ringstansmes hebben invloed.
(8) Tegelijkertijd is de verdeling van de grondstoffen binnen de compressiekamer ongelijkmatig.
2. De kwaliteit van voer en pellets wordt over het algemeen geanalyseerd op basis van hun interne en externe eigenschappen. Als productiesysteem zijn we meer blootgesteld aan zaken die verband houden met de externe kwaliteit van voerpellets. Vanuit productieperspectief kunnen de factoren die de kwaliteit van aquatische voerpellets beïnvloeden, grofweg als volgt worden samengevat:
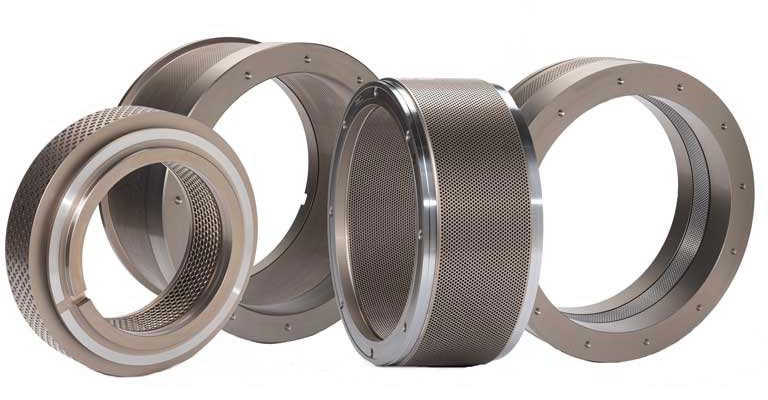
(1) Het ontwerp en de organisatie van formules hebben een directe impact op de kwaliteit van de pellets voor aquatisch voer, die goed zijn voor ongeveer 40% van het totaal;
(2) De intensiteit van het vermalen en de uniformiteit van de deeltjesgrootte;
(3) De diameter, compressieverhouding en lineaire snelheid van de ringvorm hebben invloed op de lengte en diameter van de deeltjes;
(4) De compressieverhouding, lineaire snelheid, afschrik- en ontlaateffect van de ringvorm en de invloed van het snijblad op de lengte van de deeltjes;
(5) Het vochtgehalte van de grondstoffen, het tempereffect, de koeling en het drogen hebben invloed op het vochtgehalte en het uiterlijk van de eindproducten;
(6) De apparatuur zelf, de procesfactoren en de effecten van het blussen en ontlaten hebben invloed op het gehalte aan deeltjespoeder;
3. Behandelingsmaatregelen:
(1) Pas de lengte, breedte en hoek van de stoffen schraper aan en vervang de versleten schraper.
(2) Let op het tijdig aanpassen van de positie van het snijblad aan het begin en tegen het einde van de productie vanwege de kleine toevoerhoeveelheid.
(3) Zorg tijdens het productieproces voor een stabiele toevoersnelheid en stoomtoevoer. Als de stoomdruk laag is en de temperatuur niet kan stijgen, moet deze tijdig worden aangepast of gestopt.
(4) De afstand tussen derolschaalPlaats na de nieuwe mal nieuwe rollen en repareer direct het oneffen oppervlak van de aandrukrol en de ringmal als gevolg van slijtage.
(5) Repareer het geleidingsgat van de ringvorm en reinig het verstopte vormgat zo snel mogelijk.
(6) Bij het bestellen van de ringmal kan de compressieverhouding van de drie rijen gaten aan beide uiteinden van de axiale richting van de originele ringmal 1-2 mm kleiner zijn dan die in het midden.
(7) Gebruik een zacht snijmes met een dikte van 0,5 tot 1 mm om een zo scherp mogelijke rand te garanderen, zodat deze op de raaklijn tussen de ringvorm en de drukrol ligt.
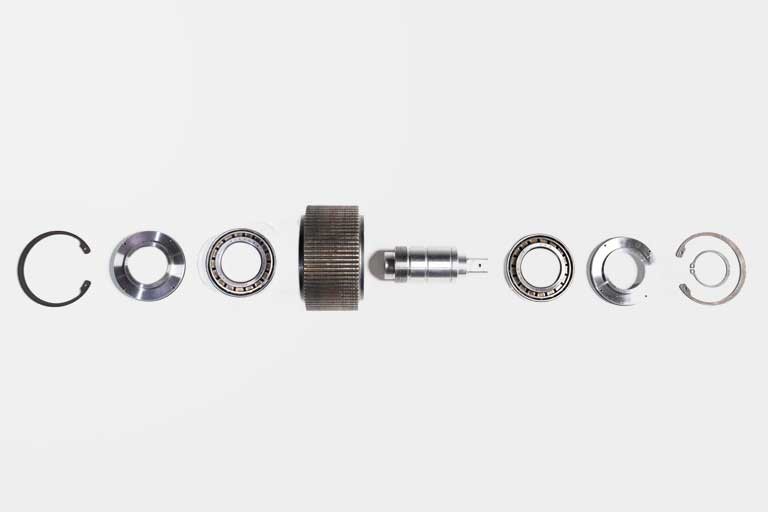
(8) Zorg voor de concentriciteit van de ringvorm, controleer regelmatig de spindelspeling van de granulator en pas deze indien nodig aan.
6、 Samenvatting Controlepunten:
1. Maalproces: De fijnheid van het malen moet worden gecontroleerd volgens de specificatievereisten
2. Mengen: De uniformiteit van het mengen van de grondstoffen moet worden gecontroleerd om de juiste menghoeveelheid, mengtijd, vochtigheidsgehalte en temperatuur te garanderen.
3. Rijping: De druk, temperatuur en vochtigheid van de puffmachine moeten worden gecontroleerd
De grootte en vorm van het deeltjesmateriaal: er moeten geschikte specificaties voor persvormen en snijbladen worden gekozen.
5. Watergehalte van het afgewerkte voer: Het is noodzakelijk om de droog- en koeltijd en -temperatuur in acht te nemen.
6. Olie spuiten: Het is noodzakelijk om de precieze hoeveelheid olie te spuiten, het aantal sproeiers en de kwaliteit van de olie te controleren.
7. Zeven: Selecteer de grootte van de zeef volgens de specificaties van het materiaal.
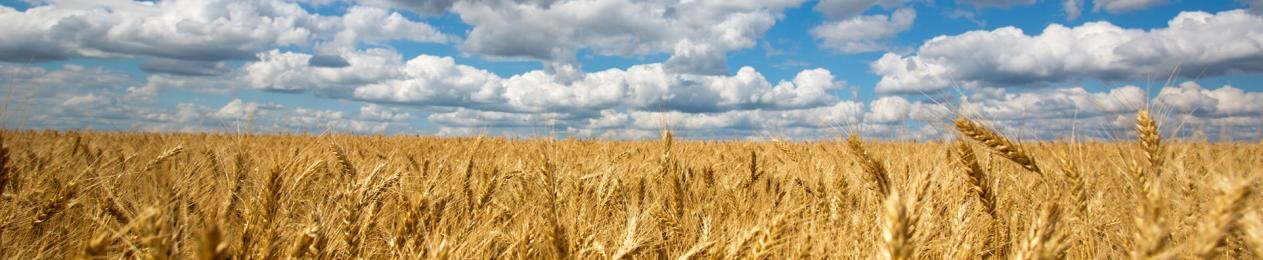
Plaatsingstijd: 30-11-2023